Introduction
In manufacturing, rhythm matters. When your production line is out of sync with demand, the results can be costly: either waste from overproduction or missed sales due to underproduction. At the core of balancing this equation is a deceptively simple but powerful concept: Takt Time.
Takt Time is defined as the maximum amount of time you can spend producing one unit of product in order to meet customer demand. It is not a productivity target or a machine speed. It is a planning metric derived from the customer's required pace of delivery. In short, it sets the tempo for production in the same way a conductor sets the pace for an orchestra.
Mathematically, it's expressed as:
Takt Time = Available Production Time / Customer Demand
If your customer needs 480 units per day, and you operate for 8 hours (28,800 seconds), then your takt time is 60 seconds. This means you must complete one unit every 60 seconds to perfectly match demand without building up inventory or falling short.
Why Takt Time Is Crucial in Manufacturing
Takt time is a cornerstone of Lean Manufacturing. It directly influences how production lines are balanced, how resources are allocated, and how continuous improvement is structured. Unlike generic efficiency metrics, takt time serves a specific purpose: it aligns your production output with actual customer needs, helping you avoid two of Lean’s biggest wastes, overproduction and waiting.
Takt time also creates visibility and accountability. It becomes a reference point for real-time performance monitoring, supporting tools like visual management boards, Andon systems, and standardized work procedures. When used correctly, it drives consistency, exposes bottlenecks, and enables systematic problem-solving.
From an operations management perspective, takt time is the starting point for line design, staffing models, shift scheduling, and even strategic decisions such as automation investment or SKU rationalization. It forces clarity between what is possible and what is necessary.
What You’ll Learn in This Article
This guide aims to be the most comprehensive resource on takt time available today. Whether you are new to the concept or already applying Lean principles, this article will walk you through the full spectrum of takt time, both in theory and in practice.
We will begin by breaking down the basic definitions and calculations, then move into advanced applications across different industries, technologies that support takt time, and how it is used strategically in line design and workforce planning. Along the way, we will reference real-world case studies and highlight common pitfalls that organizations encounter.
By the end of this article, you will not only understand takt time. You will be equipped to implement it, teach it, and challenge your teams to manage operations around it.
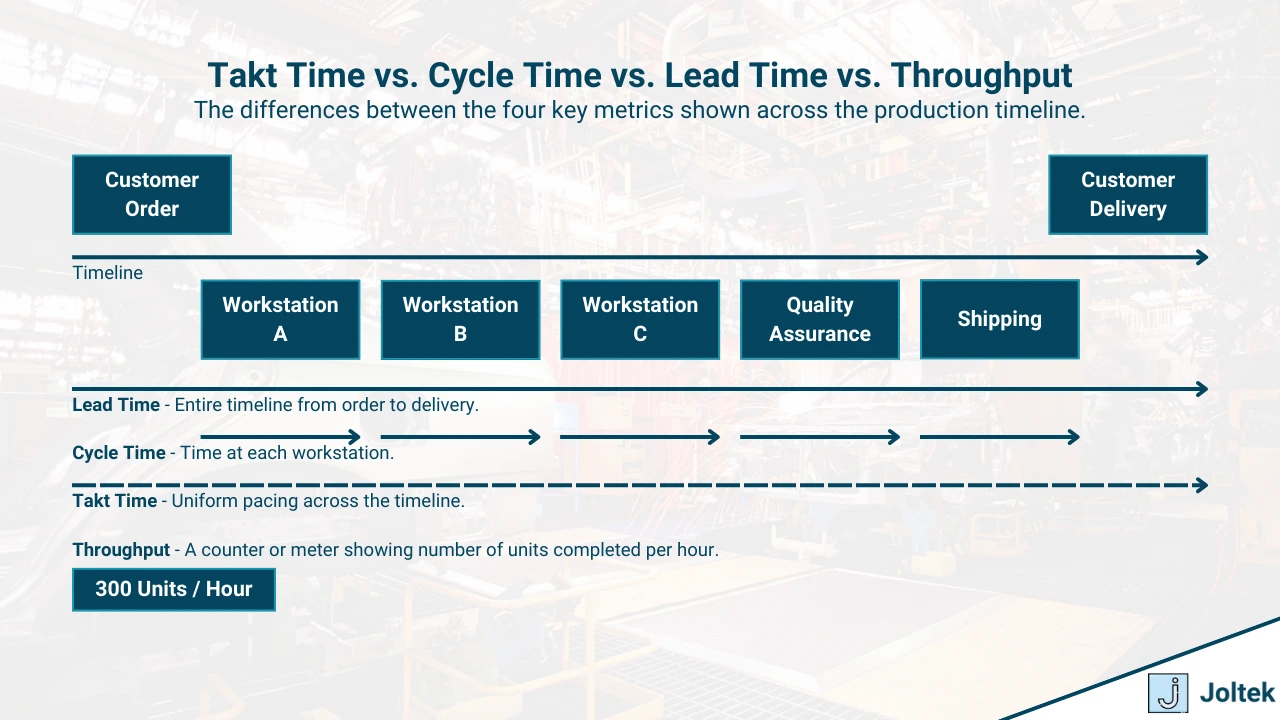
Understanding Takt Time
What Is Takt Time?
Takt time is one of the foundational concepts in Lean Manufacturing. It defines the rate at which a product must be completed in order to meet customer demand. You can think of it as the beat or rhythm that production should follow. Every operation, process, and workstation aligns to this tempo to maintain a smooth and predictable flow of work.
The word “takt” originates from the German term for “pulse” or “baton,” similar to how a conductor sets the rhythm for an orchestra. The concept was further developed and adopted by Japanese manufacturers, particularly within the Toyota Production System. It is a guiding principle that ensures production is customer-focused and paced according to real demand.
Importantly, takt time is not the same as how fast your machines run or how quickly an operator can assemble a product. It is not an efficiency target. Instead, it represents the maximum amount of time you can spend producing each unit to stay in sync with what the customer actually needs.
The formula is straightforward:
Takt Time = Available Production Time / Customer Demand
For example, if a plant operates for 7.5 hours per shift (which is 27,000 seconds), and customer orders are 900 units per day, then:
27,000 seconds / 900 units = 30 seconds per unit
This means your team must produce one unit every 30 seconds to meet the demand without overproducing or falling behind.
Takt time is typically calculated for a specific product or product family, and it serves as the heartbeat of your production system.
How Takt Time Differs from Cycle Time and Lead Time
Takt time is often confused with two other key metrics: cycle time and lead time. While they are related, they serve different purposes and are used at different levels of planning.
- Takt Time is a planning metric. It defines how often a unit must be produced to satisfy demand.
- Cycle Time is a performance metric. It measures how long it actually takes to produce one unit at a given station or process.
- Lead Time is a customer-facing metric. It measures the total time from order to delivery, including all delays and handoffs.
In a well-optimized operation, your actual cycle time should be equal to or slightly below takt time. This ensures that you are producing fast enough to meet demand, but not so fast that you generate waste. If cycle time consistently exceeds takt time, it is a clear sign of bottlenecks or inefficiencies. If it is significantly lower, it may indicate overproduction or underutilized capacity.
Why Takt Time Matters
Ensures Alignment with Customer Demand
Takt time forces operations to focus on actual demand. Instead of producing as much as possible, or reacting to vague forecasts, it grounds your schedule in what customers are actively asking for. This alignment enables just-in-time delivery, minimizes unnecessary inventory, and improves responsiveness.
Prevents Overproduction and Underproduction
Overproduction is one of the most expensive forms of waste. It ties up resources, consumes storage space, and increases the risk of scrap or obsolescence. Underproduction, on the other hand, leads to late deliveries, customer dissatisfaction, and lost revenue. Takt time helps avoid both by serving as a boundary for output.
Enables Balanced Workflow and Resource Allocation
Takt time is the foundation for designing balanced production lines. Each workstation is sized and staffed so it can complete its task within the takt window. This reduces waiting, overburdening, and uneven workloads. It also makes it easier to identify and eliminate bottlenecks. When every part of the system moves to the same tempo, efficiency improves, quality stabilizes, and teams can collaborate more effectively.
Takt Time vs. Other Metrics
Takt time is one of several important time-based measurements used in manufacturing. While it sets the pace for production, it is often confused with other metrics like cycle time, lead time, and throughput. Each of these terms plays a unique role in how production systems are planned, executed, and evaluated. Understanding the differences is critical to improving efficiency and delivering value to customers.
Takt Time vs. Cycle Time
Takt time tells you how often you need to produce a product to meet customer demand. Cycle time, on the other hand, measures how long it actually takes to produce that product at a specific process or workstation.
Takt time is derived from customer demand and available production time. It is a target based on planning. Cycle time is an observation of current performance based on how long your process takes from start to finish.
In a perfect system, your cycle time should be equal to or slightly less than your takt time. This indicates that you're working at the right pace. If your cycle time is greater than takt time, you're not producing fast enough and may miss demand. If your cycle time is shorter, you're producing too quickly, which could lead to overproduction, unnecessary inventory, and wasted resources.
In practice, takt time helps you define what your cycle time should be. Measuring both allows you to identify gaps and improvement opportunities.
Takt Time vs. Lead Time
Lead time measures the total time it takes for a customer order to move through your entire system, from order entry to delivery. This includes all steps in the process: waiting, batching, transport, inspection, and even idle time.
Takt time, by contrast, is strictly concerned with the pace of production. It does not include delays, transportation, or administrative tasks. It is based on what needs to happen on the shop floor to stay aligned with demand.
While takt time helps schedule production at the right pace, lead time reveals how long customers actually wait. A factory can have perfect takt adherence and still have long lead times if there are bottlenecks in order processing or delays in shipping. That’s why both metrics must be tracked. Takt time drives internal discipline, while lead time impacts the customer experience.
Takt Time vs. Throughput
Throughput refers to the actual number of units produced in a given period of time—say, per hour or per shift. It is a measure of output, while takt time is a measure of pacing.
If your takt time is 60 seconds, that means you need to produce one unit every 60 seconds to meet demand. In other words, your target throughput is 60 units per hour. If your actual throughput is lower than that, you're falling short. If it's significantly higher, you might be overproducing.
Takt time sets the rhythm. Throughput tells you how much you're actually delivering. Comparing the two helps assess whether you're ahead, behind, or perfectly in tune with your demand-driven goals.
When viewed together, takt time, cycle time, lead time, and throughput provide a full picture of operational performance. Takt time defines the tempo. Cycle time shows how each step is performing. Lead time tells you how long customers are waiting. Throughput confirms whether you're meeting your goals. Understanding these distinctions equips manufacturers to drive meaningful improvement, not just more activity, but more value.
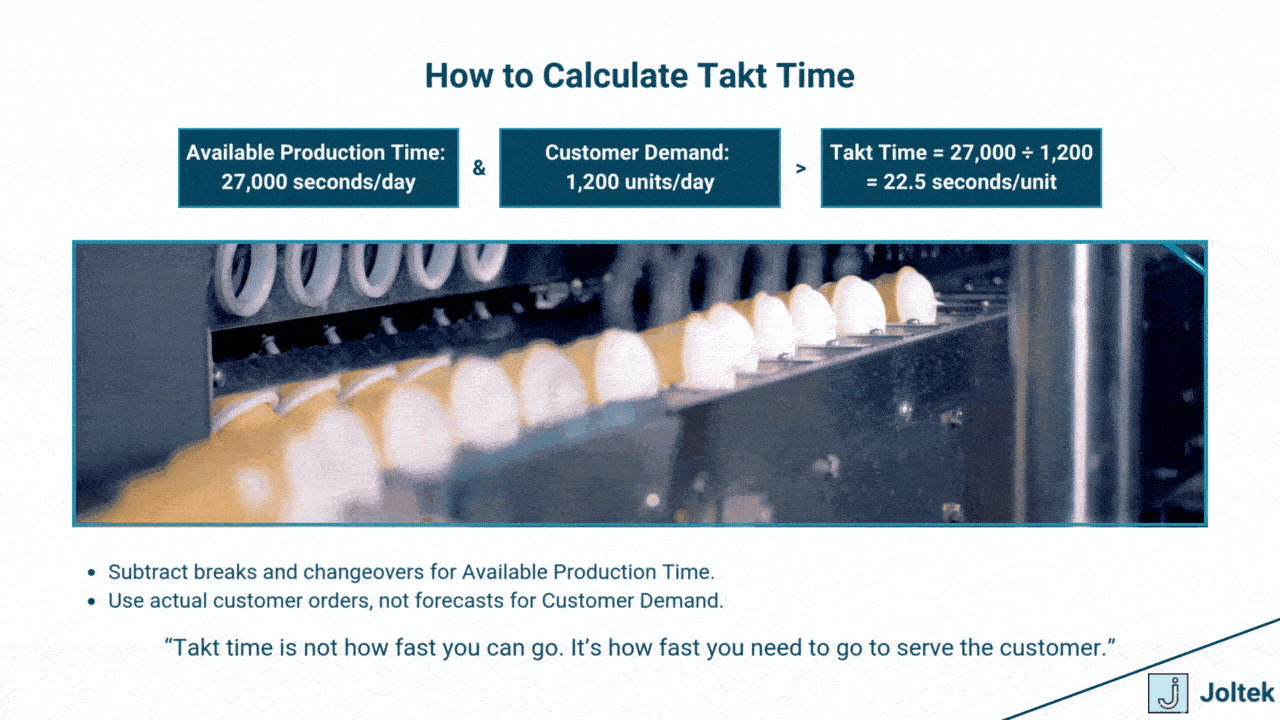
How to Calculate Takt Time
Takt time is simple in concept but requires careful consideration when applied in a real manufacturing environment. Calculating it correctly ensures your production systems are aligned with customer expectations and operational realities. In this section, we’ll walk through a practical example and explore how to adjust for real-world conditions like shift structures, downtime, and demand variability.
Step-by-Step Example
Let’s begin with a simple example. Imagine you’re managing a packaging line that must fulfill 1,200 customer orders per day.
Your production operates on one shift:
- Shift length: 8 hours
- Breaks: Two 15-minute breaks
- Total available time: 8 hours – 30 minutes = 7.5 hours = 450 minutes = 27,000 seconds
To calculate takt time:
Takt Time = Available Production Time / Customer Demand
Takt Time = 27,000 seconds / 1,200 units = 22.5 seconds per unit
This means your line needs to produce one unit every 22.5 seconds to meet demand. Every station on that line, every operator, and every machine must be capable of completing their assigned task within that window to maintain flow.
Accounting for Realistic Conditions
In actual operations, things rarely run as cleanly as textbook examples. Let’s layer in a few more practical considerations:
Variable Shift Lengths
You may run two shifts, or a combination of weekdays and weekends. If the demand target is weekly rather than daily, you would use total weekly production hours instead. Always align the denominator of your calculation (customer demand) to the same time frame used for your available production time.
Breaks and Planned Downtime
Don’t forget to subtract breaks, maintenance windows, or shift changeovers. Only include time when production is expected to run. Takt time should reflect the actual productive time available, not just the clock hours.
For example, if you run 3 shifts at 8 hours each, but lose 45 minutes per shift to breaks, meetings, and cleaning, your available production time is not 24 hours. It is 22.75 hours, or 81,900 seconds.
Changeovers and Setup
In high-mix environments, frequent changeovers can eat into available time. You may want to subtract average setup time or use weighted takt calculations across product families. This helps you avoid underestimating the true pacing needed.
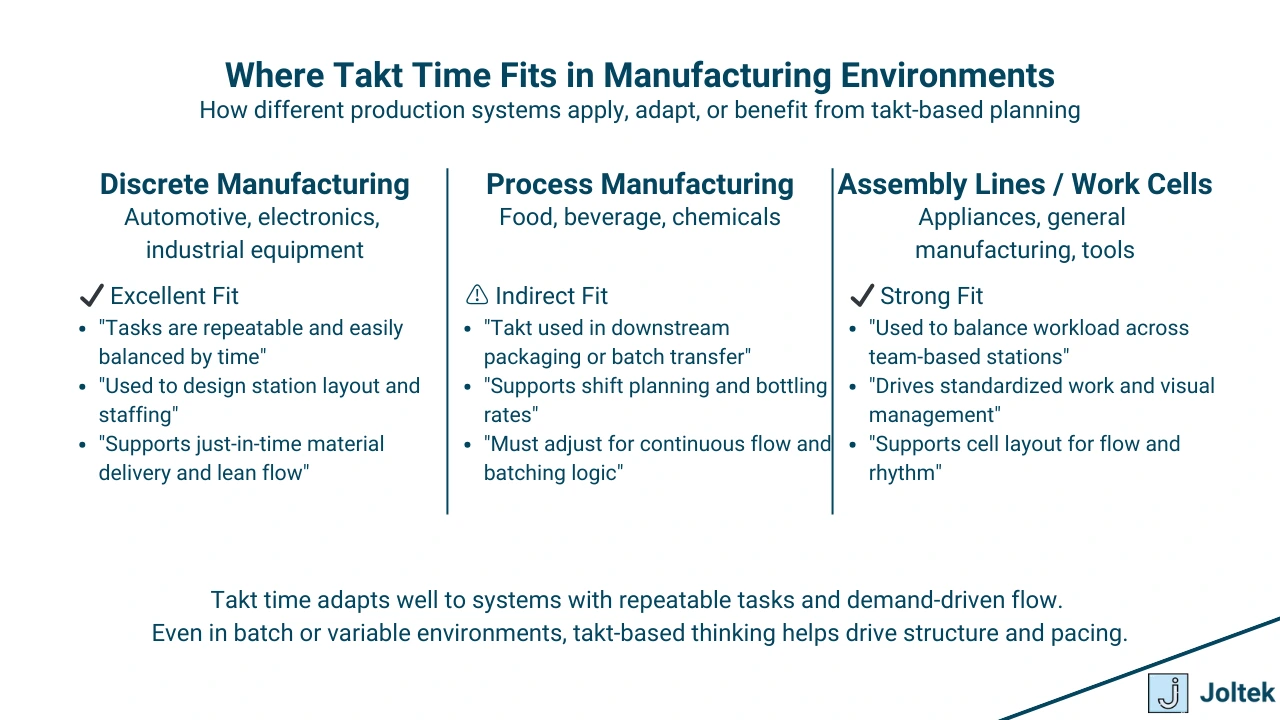
Adjusting for Variability
Takt time is based on customer demand. But what happens when demand isn’t stable?
Demand Fluctuation
If customer orders vary from day to day, calculating takt time for each shift may be impractical. Instead, use historical averages to calculate a rolling takt time. This can be based on:
- Weekly average demand
- 30-day trailing demand
- Forecasted demand from sales or supply chain teams
This approach smooths out spikes while keeping your operations aligned with trends, not just one-off orders.
Dynamic Takt
Some advanced operations use dynamic takt, an adjusted pacing that recalculates every hour or shift using real-time data. This method requires connected systems such as MES or production analytics tools and works well when you're dealing with frequent changes in volume, product mix, or downtime.
Dynamic takt allows more flexibility but requires a high level of digital maturity and disciplined process control to avoid confusion on the shop floor.
Final Thought
Getting the takt time calculation right is foundational. It defines how you organize work, schedule people, design stations, and monitor performance. But it is not static. As customer needs change, takt time should be revisited and recalculated regularly. In many lean organizations, this becomes part of daily or weekly performance reviews.
Takt Time in Practice
Takt time is more than a formula on paper. It is a practical tool that shapes the daily rhythm of production and supports lean thinking throughout an organization. When applied correctly, it creates alignment between people, machines, and customer expectations. This section explores how takt time functions in real manufacturing environments and how it supports key lean principles.
Applications Across Manufacturing
Discrete Manufacturing
Industries such as automotive, aerospace, and electronics use takt time as a foundational principle in line design and scheduling. These operations often involve structured assembly processes with clear task sequences and predictable demand. Takt time becomes the reference point for designing each workstation, staffing levels, and shift scheduling.
For example, in automotive plants, takt time might be calculated from projected daily demand and used to structure every step of the assembly line. Every operator, tool, and material movement is synchronized to this rhythm. Deviations from takt are used as immediate signals for problem-solving.
Process Manufacturing
In batch or continuous-flow environments such as food and beverage, chemicals, or pharmaceuticals, takt time is less straightforward but still useful. While you cannot always apply takt time directly to processes that do not involve discrete units, it can still inform downstream operations like packaging, labeling, and palletizing.
For example, a beverage company may use takt time to schedule its bottling lines. If customer demand calls for 90,000 bottles per shift, takt time helps determine how fast the packaging line must run, even if the liquid-filling stage is continuous.
Assembly Lines and Work Cells
In high-volume environments, takt time provides the framework for work cell design. By dividing tasks so that each operator can complete their work within the takt interval, manufacturers can reduce variability, minimize motion, and improve flow.
Work cells built around takt time are easier to manage and scale. They also simplify training, since every role is tied to a repeatable task set within a fixed time window. This discipline supports quality, safety, and team coordination.
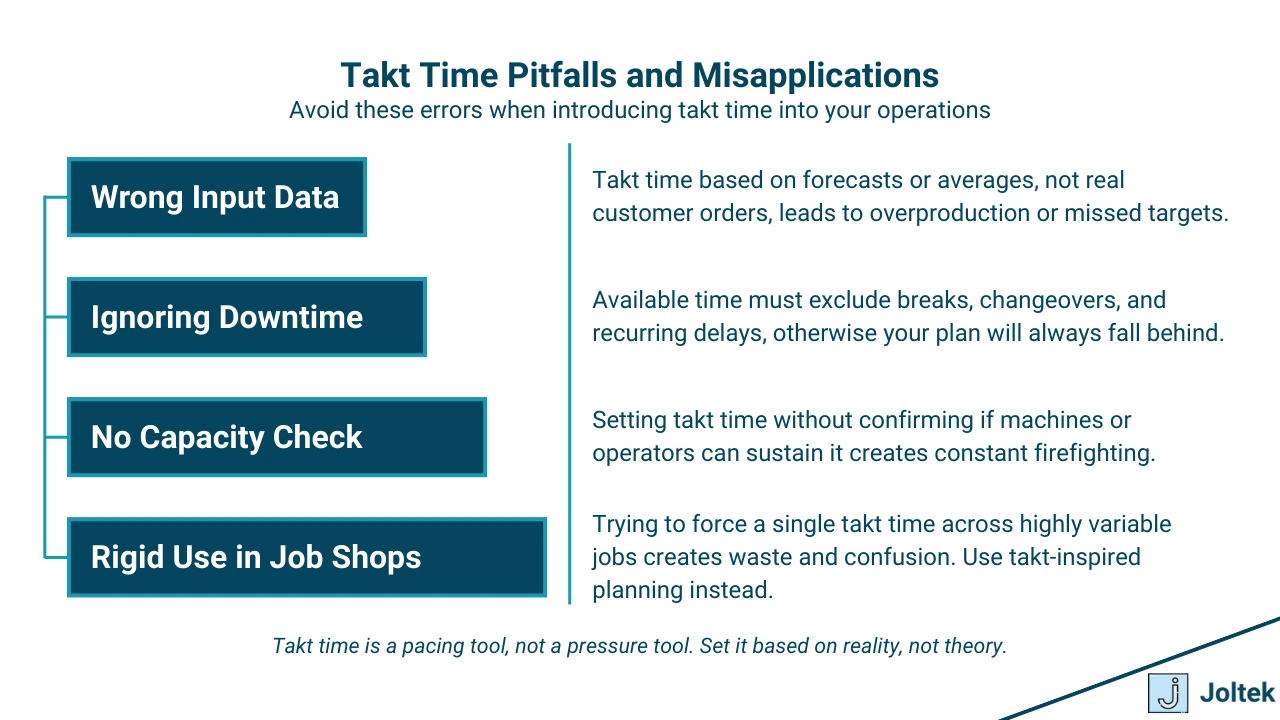
How Takt Time Drives Lean Manufacturing
Waste Identification
Takt time brings visibility to some of the most common forms of operational waste. If your cycle time is shorter than your takt time, you are likely overproducing. This results in excess inventory, higher handling costs, and increased risk of scrap. If your cycle time is longer than takt time, you are under-producing and potentially delaying customer orders.
By setting a clear benchmark, takt time allows frontline teams to identify when and where waste occurs. It becomes easier to see when production is ahead, behind, or out of sync.
Value Stream Mapping
When creating a value stream map, takt time provides the reference for comparing different processes and spotting imbalances. It helps you assess whether each operation contributes value at the right speed, or if delays, queues, or rework are causing friction.
In future-state planning, takt time becomes the tempo for designing more efficient and balanced workflows. It ensures that each step in the process is aligned with actual customer needs, not just internal capacity.
Visual Management and Takt Boards
Takt time is often made visible through visual management tools like whiteboards, magnetic takt boards, or digital dashboards. These tools track how many units should have been completed at each hour or shift, compared to how many actually were.
For instance, a team may have a board with hourly takt targets. If they fall behind, the gap becomes immediately obvious. This transparency fosters real-time accountability and encourages teams to respond proactively. In more advanced systems, digital takt boards are linked to MES platforms and displayed near the production line, updating automatically as products are scanned or completed.
Takt time is not just a number. It is a unifying concept that helps manufacturers balance efficiency with customer focus. Whether used in a fast-paced automotive plant or a complex food packaging line, takt time drives discipline, improves flow, and supports continuous improvement from the ground up.
Challenges and Pitfalls
Takt time is a powerful tool, but like any tool, its effectiveness depends on how well it is applied. When misunderstood or misused, it can lead to false confidence, flawed line designs, or operational inefficiencies. This section explores some of the most common mistakes and mismatches that manufacturers encounter when applying takt time in the real world.
Common Mistakes
Setting Takt Time Without Real Customer Data
One of the most frequent errors is calculating takt time based on forecasts, internal assumptions, or arbitrary goals rather than actual customer demand. Takt time is meant to align production with what customers truly need. If the input is flawed, the entire system risks drifting out of sync.
Relying on last month’s numbers or projected volumes may be acceptable as a short-term workaround, but teams should revisit takt time regularly and tie it directly to confirmed orders, backlog, or near-term consumption trends.
Ignoring Bottlenecks or Downtime
Takt time assumes that available production time is truly usable. However, many teams forget to subtract losses from equipment failures, changeovers, or labor shortages. As a result, they calculate takt time based on theoretical availability and then wonder why the operation keeps falling behind.
If you ignore chronic downtime or systemic inefficiencies when calculating takt time, your production schedule will look good on paper but collapse in practice. This is especially dangerous in regulated or high-risk environments where missed production targets can lead to costly delays or compliance issues.
Over-Focusing on Takt Without Capacity Planning
Takt time sets the desired pace, but it does not guarantee that you have the resources or capability to meet it. Some teams calculate a takt time of, say, 40 seconds and assume they can simply assign that target to every workstation. But if your equipment or staff cannot sustain that pace without errors, quality problems or burnout will follow.
Takt time must be paired with realistic assessments of capacity. This includes staffing, training, machine capability, material availability, and even ergonomics. When those elements are overlooked, takt time becomes a source of pressure rather than a tool for flow.
Misalignment with Production Realities
Job Shops and High-Mix, Low-Volume Environments
Takt time is most effective in high-volume, repetitive production environments. In job shops or facilities that handle a wide variety of custom orders, it can be difficult or even counterproductive to apply a single takt rate across diverse products.
In these situations, the variability in cycle times, setups, and customer requirements often makes it impossible to create a consistent rhythm. Instead of forcing takt where it does not fit, manufacturers should consider takt-inspired thinking. This includes applying pacing concepts within product families or stabilizing subsets of operations that are more predictable.
Variable or Seasonal Demand
For companies with seasonal spikes or frequent changes in order volume, takt time can feel like a moving target. A fixed takt rate may become obsolete in a matter of weeks, or even days.
To address this, some operations use rolling takt averages based on recent demand, or dynamic takt systems that adjust more frequently. However, dynamic systems require discipline, robust data infrastructure, and a culture that is comfortable with change. Without that foundation, rapidly changing takt rates can cause confusion and frustration on the shop floor.
Takt time is a powerful anchor for lean systems, but it must be applied with awareness of your actual production environment. When calculated accurately and used with care, it drives alignment, flow, and customer satisfaction. When misapplied, it becomes just another number that teams ignore or work around.
The key is to treat takt time not as a rigid command, but as a living metric that must evolve with your processes, your products, and your customer expectations.
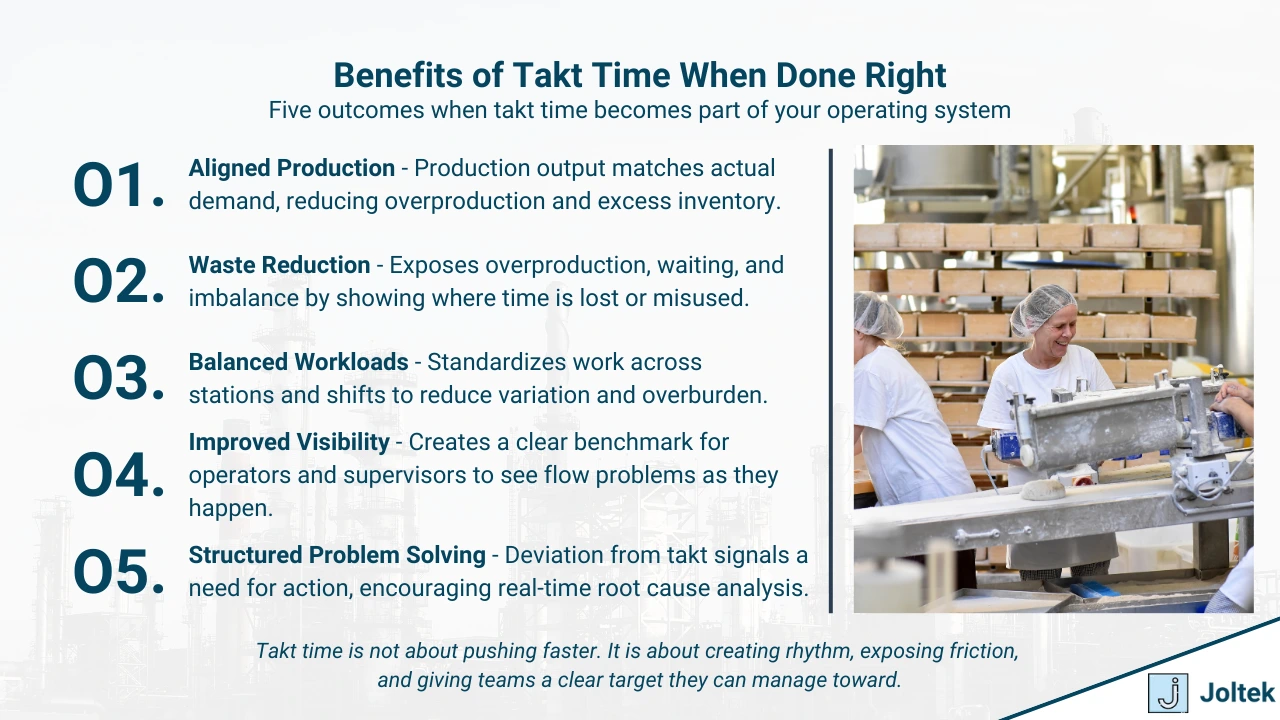
Conclusion
Takt time is not just a calculation. It is a core discipline that connects your operations directly to the needs of your customer. When properly understood and applied, it helps manufacturers control the pace of production, reduce waste, and create systems that are more predictable, stable, and efficient.
In this first part of the article, we covered the foundations of takt time. We explained what it is, how it compares to cycle time, lead time, and throughput, and how to calculate it using real production constraints. We also explored how takt time is applied across different types of manufacturing and how it supports lean initiatives such as value stream mapping, waste reduction, and visual management. Finally, we examined some of the most common mistakes and practical limitations that teams should watch for when using takt time in complex environments.
Across all of these areas, one theme remains consistent. Takt time is a guide. It does not promise perfection, but it gives your operation a clear and measurable direction rooted in customer expectations.
In the second part of this article, we will explore how modern manufacturing tools support takt-based systems, how companies use takt time in strategic planning and digital transformation efforts, and how to apply takt thinking in environments with high variability. We will also review examples from real-world case studies and examine how leading manufacturers are adapting takt time for flexible, data-driven operations.
If your organization is serious about aligning operations with demand, reducing waste, and improving flow, mastering takt time is essential. The journey starts with understanding the basics, but the impact comes from building it into the DNA of how your teams work and make decisions.